Revolutionierung des bionischen Designprozesses für die B-Säule
Die visuelle Programmierung revolutioniert den bionischen Leichtbauprozess von Hyundai, indem sie die Leistungsfähigkeit von connected engineering mit der additiven Fertigung kombiniert. Sie läutet eine neue Ära der Fahrzeugstrukturentwicklung ein, verschafft einen Vorsprung bei komplexen Optimierungsaufgaben und inspiriert mit innovativen bionischen Designkonzepten.
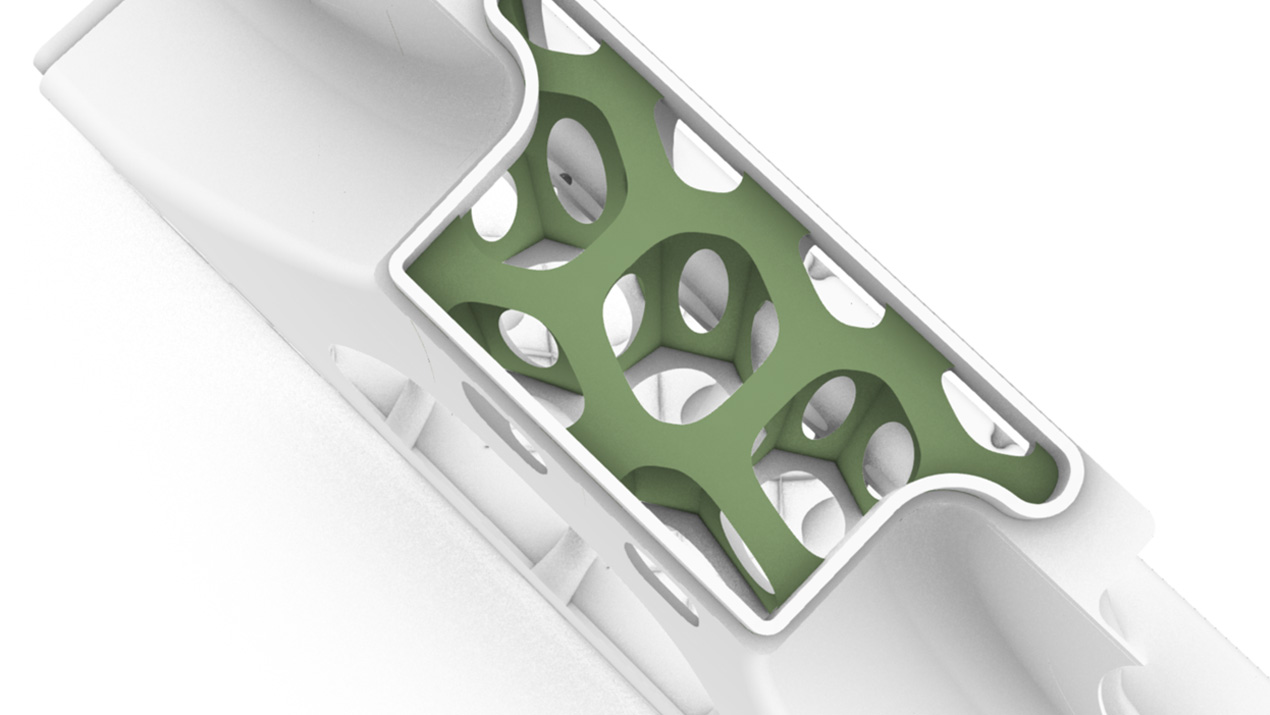
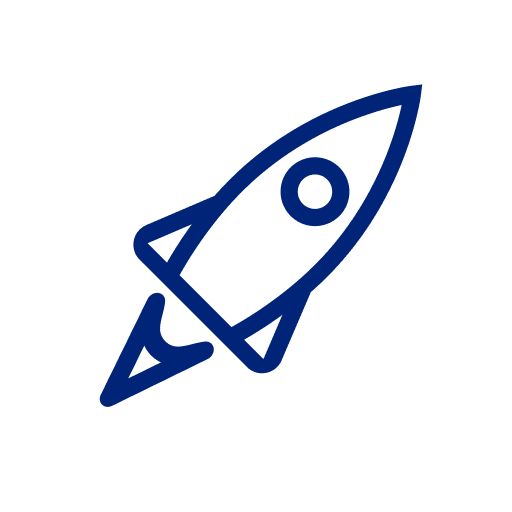
47% Gewichtsreduzierung
Verbesserte Leistung, Materialverbrauch und CO2-Emissionen
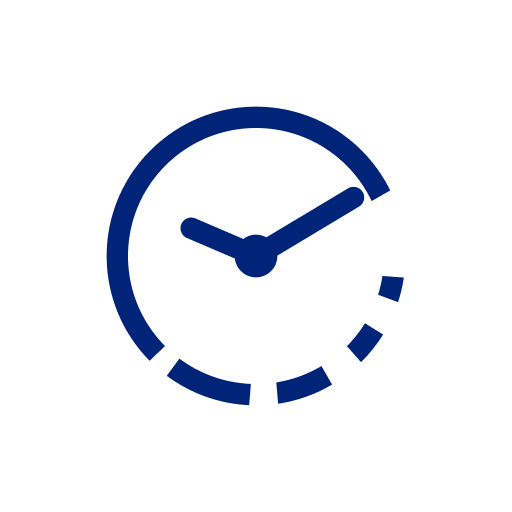
80% Zeitersparnis
Im Vergleich zum regulären Verfahren
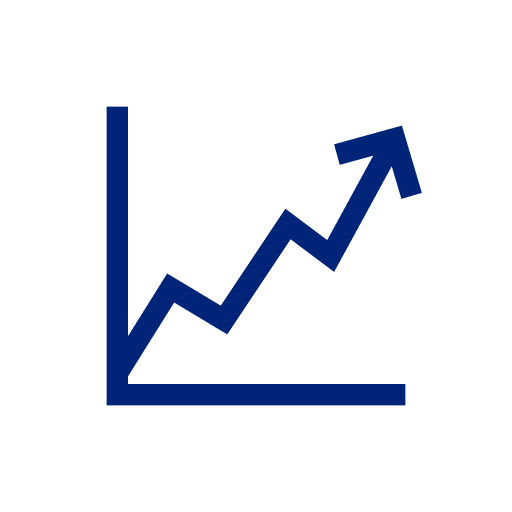
20% bessere Leistung
Verringerung des Aufprallrisikos
Challenge
Die Automobilindustrie sieht sich täglich mit neuen Herausforderungen konfrontiert, um einem sich wandelnden Umfeld gerecht zu werden, wie z. B. neuen Styling-Trends, wissenschaftlichen Entdeckungen und strengeren Emissionsvorschriften. Eine kontinuierliche Verbesserung und Weiterentwicklung von Strukturteilen ist notwendig, um Gewicht zu reduzieren und gleichzeitig Leistung und Effizienz zu verbessern.
Die B-Säulen-Verbindung ist eines der kritischen Teile der Karosserie und eine besondere Herausforderung für die Optimierung des Leichtbaus. Zum einen muss sie im Falle eines Seitenaufpralls mehrere strenge Anforderungen erfüllen, zum anderen muss sie sehr steif sein. Ziele, die nur schwer zu vereinen sind.
Aus Sicht der Fertigung bietet die additive Fertigung bereits ein hohes Potenzial für den strukturellen Leichtbau. Berücksichtigt man aber auch das Potenzial der Designfreiheit, liegt das Hauptproblem auf der Seite der Bauteilentwicklung. Denn wenn Hyundai-Ingenieure diesen Herausforderungen mit traditionellen Methoden und Softwaretools begegnen, kann die Designfreiheit nicht voll ausgeschöpft werden und iterative Prozesse zwischen Tools und Entwicklungsabteilungen sind langwierig und langsam.
Synera ist eine bahnbrechende Lösung, die den Konstruktionsprozess für die B-Säule node im Fahrzeugbau erheblich rationalisiert. Diese innovative Technologie automatisiert die Konstruktion und macht manuelle Eingriffe überflüssig. Dadurch wird nicht nur der Arbeits- und Zeitaufwand reduziert, sondern es werden auch beeindruckende Ergebnisse erzielt.
Hyundai Motor Europa Technisches Zentrum
Das HMETC (Hyundai Motor Europe Technical Center) gehört zu den weltbekannten Marken Hyundai, Kia und Genesis und ist das einzige Forschungs- und Entwicklungszentrum des Unternehmens in Europa. Die Aufgabe des HMETC ist es, sicherzustellen, dass jedes Fahrzeug die anspruchsvollen Standards der europäischen Kunden erfüllt und an die Bedürfnisse dieses speziellen Marktes angepasst ist. Mit den schnellen Fortschritten in Netzwerk und Technologie streben wir danach, die bestmöglichen Lösungen für eine bessere Zukunft zu schaffen.
Lösung
Mit dem Ansatz connected engineering war Hyundai in der Lage, den Entwicklungsprozess in einem Workflow zu digitalisieren. Dies ist die Grundlage für einen automatisierten Entwicklungsprozess, der die Entwicklungserfahrung der beteiligten Akteure und Abteilungen berücksichtigt und in Echtzeit während des Entwicklungsprozesses zur Verfügung stellt. Dieser Ansatz selbst führt zu einer deutlichen Reduzierung der Entwicklungszeit und des Aufwands.
Der automatisierte Entwicklungsprozess beginnt mit der Definition von Eingabedaten wie Materialien, Lastfällen, Leistungskriterien, Fertigungseinschränkungen und Prozesskosten. Dann wird der Designraum definiert und alle Daten werden verarbeitet, um eine Topologieoptimierung in Verbindung mit Altair Optistruct durchzuführen. Basierend auf den strukturellen Lastpfaden erstellen integrierte bionische Designalgorithmen leichte Strukturen, die speziell auf die kritischen Lastfälle zugeschnitten und parametrisch optimiert sind. Der vollparametrische CAD-Entwurf in Synera und die Datenanbindung an die externe Software erfolgen vollständig automatisch. Das Ergebnis ist also nicht ein einziger Entwurf, sondern mit Hilfe der Parameterstudie (Design of Experiments, DoE) werden am Ende des Prozesses automatisch Hunderte von verschiedenen Varianten erstellt, indem der Eingabedatensatz und die Entwurfsparameter geändert werden.
Die Hyundai-Ingenieure konnten dies als Vorsprung nutzen und komplexe Crash-Simulationen nur mit den beiden vielversprechendsten Designvarianten durchführen. Nach Erhalt der Crashergebnisse können die endgültigen Entscheidungen und Änderungen der besten Designvariante dann vom Entwickler mit nur wenigen kleinen Parameteränderungen vorgenommen werden. Während die Ingenieure früher bei jeder Änderung wieder bei Null anfangen mussten, erfordert dieser automatisierte Ansatz keine manuellen Eingriffe in das Design und führt nicht nur zu einem leistungsfähigeren Bauteil. Der Workflow bewältigt die Komplexität mehrerer Optimierungsziele mit Leichtigkeit, was zu einem leistungsfähigeren Teil führt und die Entwicklungszeit erheblich verkürzt. Letztendlich hat die Partnerschaft zwischen Hyundai und Synera den Weg für ein rationalisiertes Automobildesign geebnet und verdeutlicht das transformative Potenzial der visuellen Programmierung in der Konstruktion.
Mehr über diesen Arbeitsablauf
Vorteile
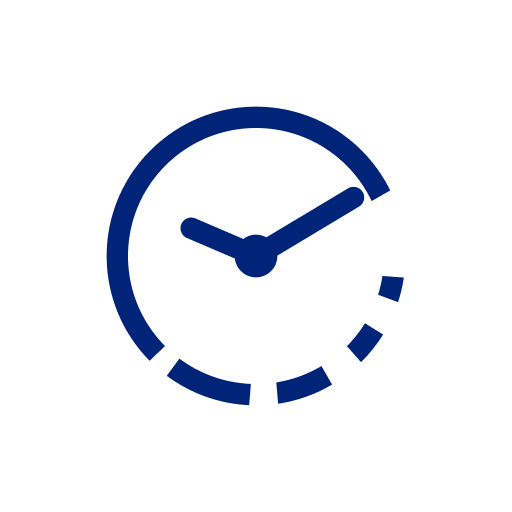
Verkürzung der Time-to-Market
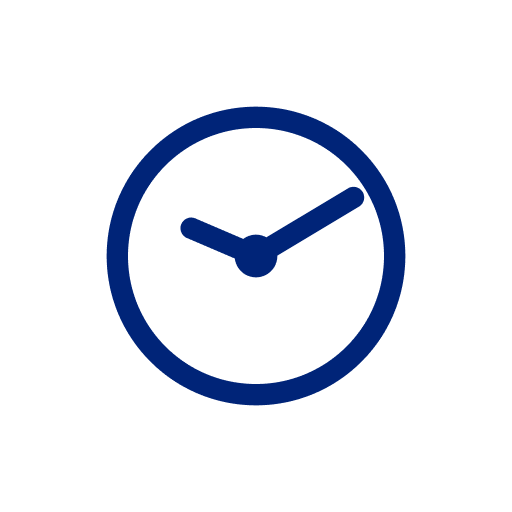
Sparen Sie Entwicklungszeit und -kosten durch Automatisierung
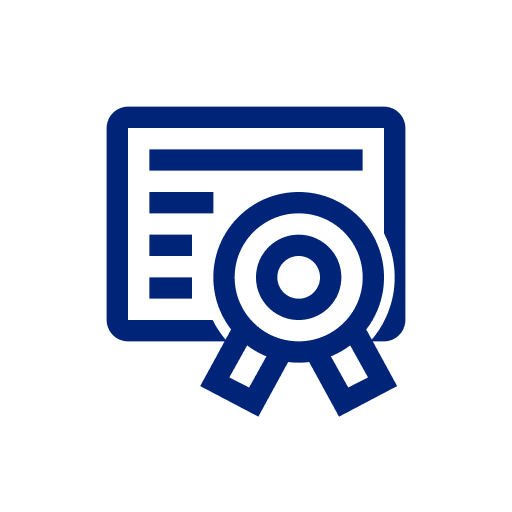
Wissensspeicherung durch Digitalisierung der Technik
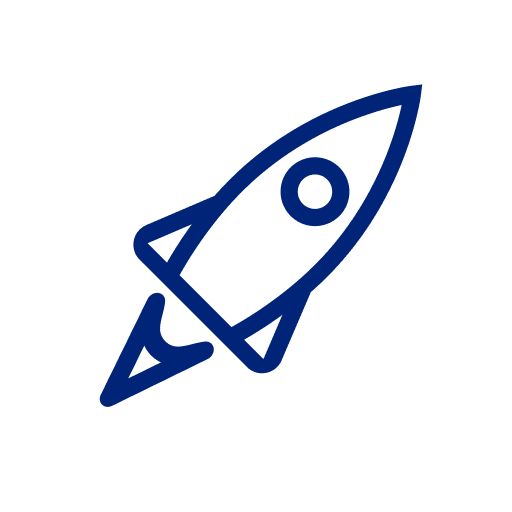
Skalierung des Engineering-Prozesses
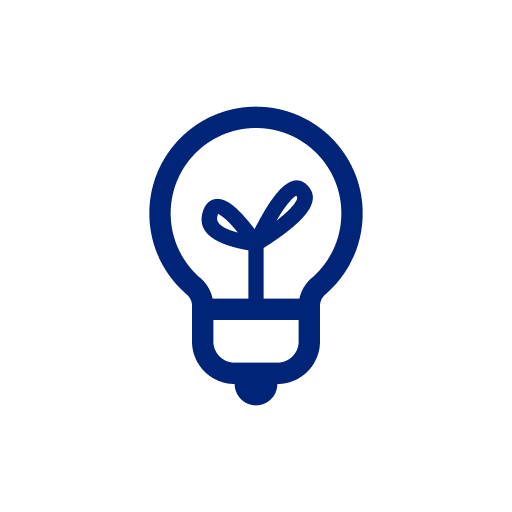
Innovative Konzepte durch algorithmischen Entwurf