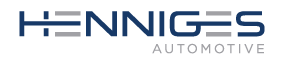
Schwingungsdämpfendes Mittellager für den Antriebsstrang
Automatisierte Entwicklung für den Druckguss
Der Entwicklungsprozess von Druckgussteilen ist durch manuelle Prozessiterationen stark eingeschränkt. Die Digitalisierung und Automatisierung des Prozesses führt zu immensen Einsparungen und einer effizienten Strategie für die Teileentwicklung der Zukunft.
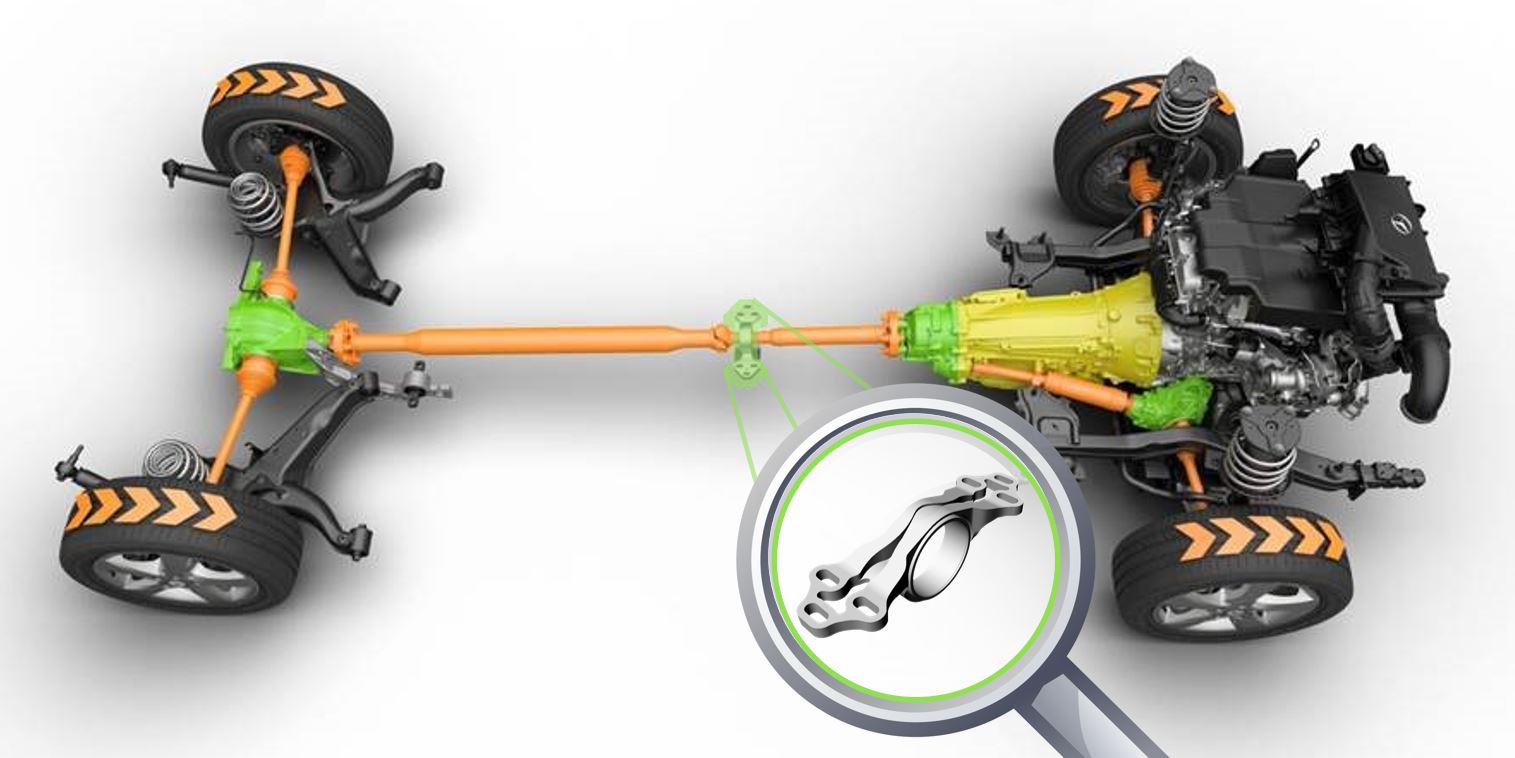
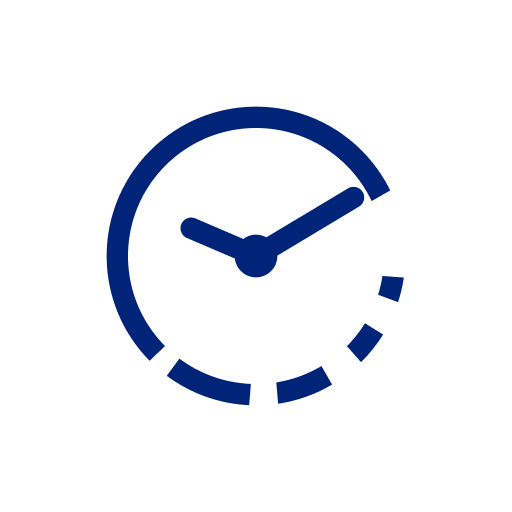
80% Zeitersparnis
Im Vergleich zu einer klassischen Entwicklung
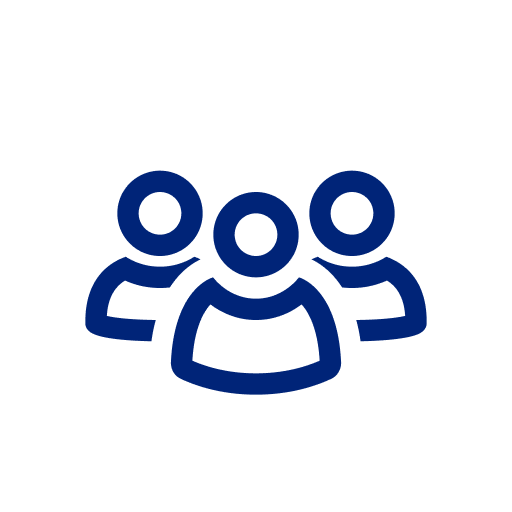
85% Wiederverwendbarkeit
Kopieren und Einfügen des Arbeitsablaufs für ähnliche Teile
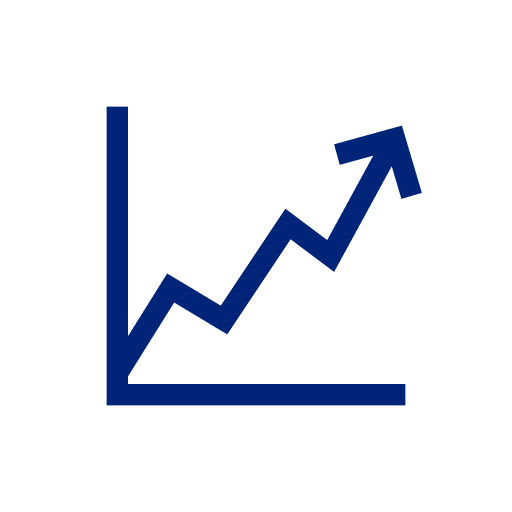
18% weniger Gewicht
Verbesserte Leistung und Materialeinsparung
Challenge
Der Konstruktionsprozess des Mittellagers für den Antriebsstrang eines Transporters umfasst Konstruktions-, Simulations- und Optimierungsschritte und ist kein geradliniger Prozess, sondern beinhaltet viele manuelle Iterationen. Um das Bauteil an die Leistungsanforderungen anzupassen oder auf Änderungen der Eingabedaten zu reagieren, die häufig auftreten, muss die CAD-Konstruktion immer wieder angepasst werden. Und damit verbundene Validierungsschritte müssen ebenfalls wiederholt werden. All dies bedeutet einen hohen manuellen Aufwand, insbesondere für den Konstrukteur.
Henniges Automotive
Henniges beliefert Automobil-Erstausrüster (OEMs) mit Dichtungssystemen für Türen, Fenster, Kofferräume, Heckklappen, Schiebedächer und Motorhauben. Außerdem beliefert das Unternehmen den Automobilmarkt mit vibrationsdämpfenden Komponenten und gekapselten Glassystemen. Henniges hat seinen Hauptsitz in Auburn Hills, Michigan, und beliefert alle großen OEM-Kunden der Automobilindustrie. Das Unternehmen unterhält Niederlassungen in Nordamerika, Südamerika, Europa und Asien und beschäftigt weltweit über 8.000 Mitarbeiter.
Lösung
Henniges Automotive verfolgte den Ansatz, die Connected Engineering um die Entwicklungsprozesse für die Konstruktion des Mittellagers im Druckguss zu beschleunigen. Synera's Connected Engineering ermöglicht es, digitalisierte Engineering-Aufgaben wiederholt zu verwenden. Dies wurde erreicht, indem der Entwicklungsprozess in der visuellen Programmierplattform digitalisiert wurde.
Der Arbeitsablauf basiert auf Eingabedaten aus Excel, umfasst einen parametrischen CAD-Entwurf, eine automatische Rekonstruktion der Topologieoptimierung innerhalb von Synera und die Verbindung zu Altair Optistruct für die Topologieoptimierung und FEA-Validierung, wobei der Schwerpunkt auf dem Datenaustausch in Echtzeit liegt. Der Entwicklungsprozess wird automatisch durchlaufen, so dass Validierungsiterationen, Änderungen der Eingabedaten in letzter Minute und die damit verbundenen Neukonstruktionen ohne manuelle Eingriffe durchgeführt werden - ein revolutionärer Durchbruch im Bauwesen.
Mehr über diesen Arbeitsablauf
Vorteile
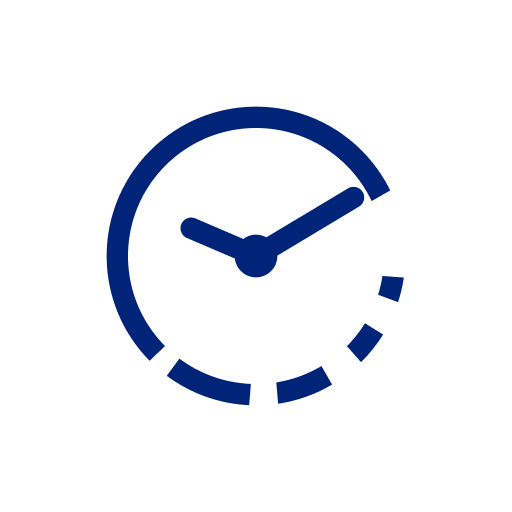
Verkürzung der Time-to-Market
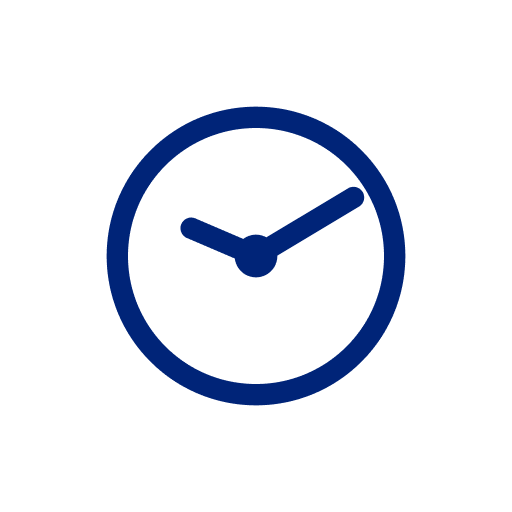
Sparen Sie Entwicklungszeit und -kosten durch Automatisierung
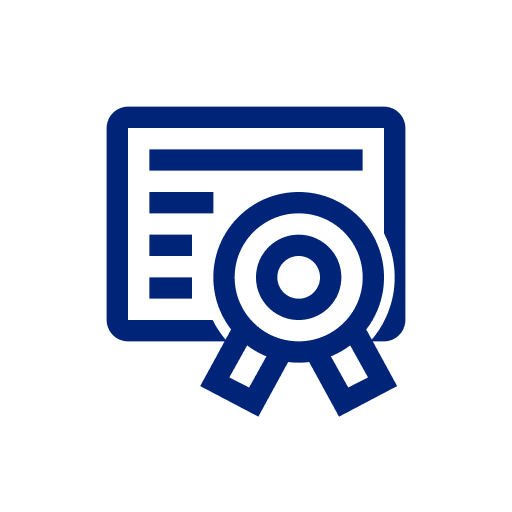
Wissensspeicherung durch Digitalisierung der Technik
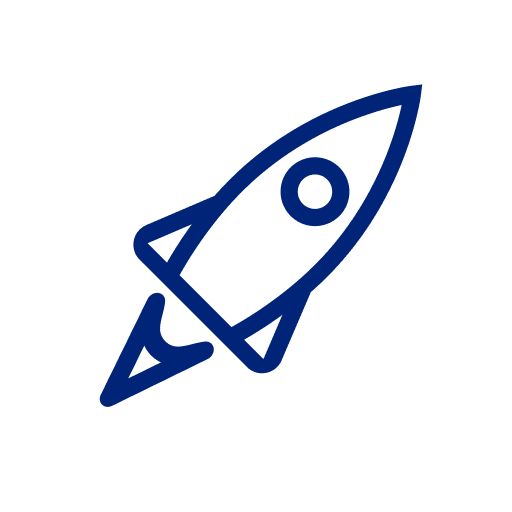
Skalierung des Engineering-Prozesses
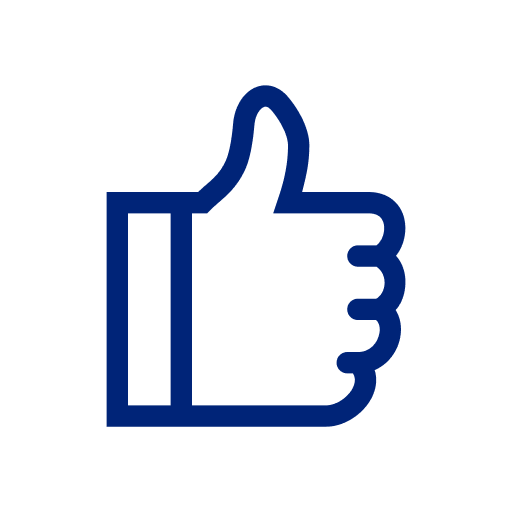
Zusammenspiel mehrerer Engineering-Tools